
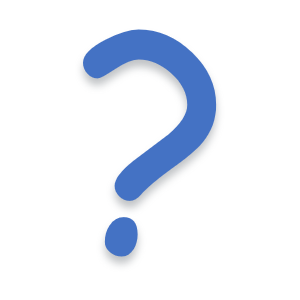
You’re in the wrong sub.
You’re in the wrong sub.
You didn’t list the hardware or what the temps used to be before this. Assuming it’s a recent increase from sane normals, your best course of action is to move the system, give it a thorough cleaning, and change the thermal interface material. Underclock / undervolt is a temporary solution as inadequate heat dissipation can still occur even if the temps appear normal, degradation will continue.
You won’t brick the computer by moving it and changing the thermal paste. If you’re not confident enough, just watch a video or two online about how to handle the system, I bet there’s videos of your specific hardware out there. You’re more likely to incorrectly configure the hardware via software controls than you are to damage it by swapping the thermal paste.
Thank you, I was so confused and stuck lol. I always just treated the top as the starting spot because the days starts at 12:00 AM. That’s what I get for trying to think through this well past my bedtime 🤣
What?
Two, Eight, Eleven, — not gonna type it all out because it’s already wrong.
What am I missing here?
I was taught that bat shit (guano) is toxic to humans in ways that can make the person “go crazy” before they die. Similar to mercury poisoning and being a “mad hatter” from the days of mercury lined headwear.
Yeah, soft serve is just frozen sugar milk, comes in cartons like regular milk and you can totally just drink it, tastes a bit like whole milk but clearly with an unhealthy amount of sugar in it.
They first started selling hamburgers in 1958.
The wiki has all the info you need.
Since you’re asking for opinions, I think you might be overreacting. But that’s totally natural after an accident!
That said, if you’re considering never driving again, then you really have to be sure that’s possible. If your family pushed you into it in the first place, they might already know that it isn’t feasible to rely on public transport where you live. That is extremely common in the US, because there is so much damn space between everything in most places. If you have to rely on others to fill the gaps where public transit fails, then you have to really consider if you’re doing more harm than good by refusing to drive. Ultimately the decision is up to you but there’s lots to consider here that we don’t have all the information for. It’s a good skill to have but requires maintenance to keep.
Dev betas usually have a LOT more logging and background processes running and battery life is expected to be worse than public stable release, especially in the first couple days after install while all the indexes get refreshed and rebuilt globally.
Is the mother supposed to be sad about religion being a sham or sad that her child doesn’t believe? The comic is too ambiguous to me because the 1st and 2nd panel heavily imply a caricature of atheism often spread by religious people who feel powerless in their own lives.
I just want id to do something else. Doom is fun and all but they’ve kinda perfected it.
I would make the case for proxmox on the machine so you can divvy up the hardware as you see fit— but also setup the hard drives as a zfs1 pool (1 redundancy failure allowed). This way you can make multiple isolated machines or use LXC containers directly for apps, services, etc. while benefiting from ZFS’s excellent performance and reliability. I would say that TrueNAS Scale has been a bit of a letdown for me because it feels bloated, easy to make mistakes with complicated setups, and I have less control over the hardware. I don’t like how updates have fully broken apps. That said it is a reliable ZFS wrapper with more bells and whistles in the UI over what proxmox offers— caveat being that both can do everything if you want to take the time to learn ZFS commands.
There is also the TrueNAS based alternative HexOS that is more beginner friendly for just getting a nice NAS setup fast while still supporting apps / containers.
Not to mention— the value for that 30% on platform + 0% off platform cut for steam is insane. The payment processing, storage, hosting, worldwide routing and caching, multiplayer sdks and integrations, and dozens of other publisher / developer available tools are worth every single penny to have valve handling for you.
The value is there and so is the install base.
Definitely splatoon, most likely splatoon 3.
What about a hard drive made of network pings?
I love Actual. It’s fantastic and easy to use. I use off-budget accounts and weekly / monthly reconciliation just to keep the general value of these accounts at stable intervals.
I have a slight bone to pick with the PWA version of the site though. After a couple months of using the PWA front end to keep my budget and transactions accurate manually, I opened the site on my desktop browser and it completely lost all that work due to a sync issue. Apparently the PWA for weeks had not remained in sync and so all manual entries were not making back to the server. But the app works so well I never noticed because it kept just working. Supposedly there’s an alert saying it’s not synced with the server but it’s not prominent enough. So if you use that feature (the PWA) then be sure it’s syncing often.
5 because the handle isn’t a fucking nightmare and won’t be distracting to eating but also I have that exact set and only use the larger ones unless I am forced to use the smaller ones. I picked the set for these reasons.
Literally none of what that person commented with was a thought or a feeling. It was an actual fact, with proof.
So much for all those studio purchases. What a waste.